bottom bending sheet metal Air forming is the most common method of forming used today in the production of precision sheet metal parts and is listed by all major press . This guide will help you understand what is a junction box is and get the best possible junction box for yourself without any struggle when you need one. Follow the instructions, and you’ll soon find a reliable junction box!
0 · types of bending sheet metal
1 · sheet metal bending standards
2 · sheet metal bending near me
3 · sheet metal bending guidelines
4 · sheet metal bending chart
5 · problems with sheet metal bending
6 · bending sheet metal by hand
7 · bending galvanized sheet metal
Western and Wordpress - Home - Western Sheet Metal
ikea steel cabinets
Bottom bending creates reliable, accurate bends in sheet metal. Where accuracy in bend angles is important and variation between different parts in a production run needs to be avoided, bottom bending is preferable.Bottom bending, or bottoming, is a press brake operation that forms an angle in sheet metal by enclosing the sheet between the punch and the die. WILA .
This Komaspec guide provides an overview of the main sheet metal bending processes, the advantages and disadvantages of each, basic design considerations with sheet metal bending . Air forming is the most common method of forming used today in the production of precision sheet metal parts and is listed by all major press .Sheet metal bending is a highly effective process for producing parts. Learn more about sheet metal bending today!Bottom bending, also known as air bending, is a widely used technique in sheet metal fabrication where the material is bent by pressing it between a punch and a die. Unlike other bending .
ima cnc machine
Bending is a fundamental process in sheet metal working that involves deforming a metal workpiece into a desired shape by applying force between two tools by a press brake: an upper tool (known as a punch) and a bottom tool (known as a .Bottom bending is the process of stamps the radius of the punch tip into the work piece. This differs from Coining, which puts the entire surface of the work piece under such tonnage that it begins to flow. when Bottom Bending the die angle . Bottoming, also known as bottom bending or bottom pressing, is a precise sheet metal bending technique where the metal sheet is pressed against the bottom of a die to achieve a specific angle. Unlike air bending, where the . Bottom bending creates reliable, accurate bends in sheet metal. Where accuracy in bend angles is important and variation between different parts in a production run needs to be avoided, bottom bending is preferable.
Bottom bending, or bottoming, is a press brake operation that forms an angle in sheet metal by enclosing the sheet between the punch and the die. WILA offers durable and high quality precision tooling for bottom bending with 90° angles.This Komaspec guide provides an overview of the main sheet metal bending processes, the advantages and disadvantages of each, basic design considerations with sheet metal bending and material selection information.
Air forming is the most common method of forming used today in the production of precision sheet metal parts and is listed by all major press brake manufacturers worldwide as the preferred method of sheet metal bending. Bottoming is also known as bottom pressing or bottom striking. As the name “bottom pressing” suggests, the punch presses the metal sheet onto the surface of the die, so the die’s angle determines the final angle of the workpiece. With bottoming, the inner radius of the angled sheet depends on the die’s radius.Sheet metal bending is a highly effective process for producing parts. Learn more about sheet metal bending today!Bottom bending, also known as air bending, is a widely used technique in sheet metal fabrication where the material is bent by pressing it between a punch and a die. Unlike other bending methods like coining or edge bending, bottom bending allows for greater flexibility, reduced setup time, and minimal risk of damaging the material.
Bending is a fundamental process in sheet metal working that involves deforming a metal workpiece into a desired shape by applying force between two tools by a press brake: an upper tool (known as a punch) and a bottom tool (known as a V-die).Bottom bending is the process of stamps the radius of the punch tip into the work piece. This differs from Coining, which puts the entire surface of the work piece under such tonnage that it begins to flow. when Bottom Bending the die angle should match the intended angle of the work piece, adjusting a few degrees for Spring Back, hence the .
Bottoming, also known as bottom bending or bottom pressing, is a precise sheet metal bending technique where the metal sheet is pressed against the bottom of a die to achieve a specific angle. Unlike air bending, where the metal doesn’t fully conform to the die, bottoming forces the metal to make full contact with the die’s surface.
Bottom bending creates reliable, accurate bends in sheet metal. Where accuracy in bend angles is important and variation between different parts in a production run needs to be avoided, bottom bending is preferable.Bottom bending, or bottoming, is a press brake operation that forms an angle in sheet metal by enclosing the sheet between the punch and the die. WILA offers durable and high quality precision tooling for bottom bending with 90° angles.This Komaspec guide provides an overview of the main sheet metal bending processes, the advantages and disadvantages of each, basic design considerations with sheet metal bending and material selection information. Air forming is the most common method of forming used today in the production of precision sheet metal parts and is listed by all major press brake manufacturers worldwide as the preferred method of sheet metal bending.
Bottoming is also known as bottom pressing or bottom striking. As the name “bottom pressing” suggests, the punch presses the metal sheet onto the surface of the die, so the die’s angle determines the final angle of the workpiece. With bottoming, the inner radius of the angled sheet depends on the die’s radius.Sheet metal bending is a highly effective process for producing parts. Learn more about sheet metal bending today!Bottom bending, also known as air bending, is a widely used technique in sheet metal fabrication where the material is bent by pressing it between a punch and a die. Unlike other bending methods like coining or edge bending, bottom bending allows for greater flexibility, reduced setup time, and minimal risk of damaging the material.
Bending is a fundamental process in sheet metal working that involves deforming a metal workpiece into a desired shape by applying force between two tools by a press brake: an upper tool (known as a punch) and a bottom tool (known as a V-die).Bottom bending is the process of stamps the radius of the punch tip into the work piece. This differs from Coining, which puts the entire surface of the work piece under such tonnage that it begins to flow. when Bottom Bending the die angle should match the intended angle of the work piece, adjusting a few degrees for Spring Back, hence the .
types of bending sheet metal
sheet metal bending standards
sheet metal bending near me
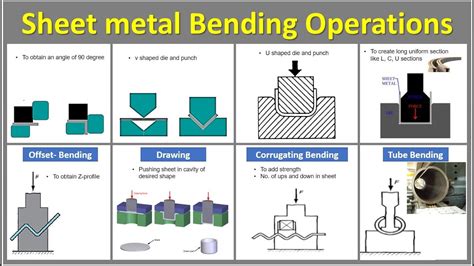
David’s educational background includes Marysville Pilchuck High School and Everett Community College, the Western Washington Sheet Metal apprenticeship program, and multiple continuing education classes through the sheet metal training center.
bottom bending sheet metal|sheet metal bending standards