welding light sheet metal Welding thin metal is challenging. There is no denying that. But, if you practice and use the tips we shared in this article, you’ll get the best chance for success. After you inevitably burn through some scrap sheets of metal and warp others, you’ll gain more experience and learn . See more Camber is the measured deviation of the side of a sheet from a straight edge. Camber is caused by one side of a sheet being elongated more than the other side during perforation or leveling. Camber often results from having unequal side margins on a sheet.
0 · welding sheet metal using mig
1 · welding sheet metal
2 · welding aluminum sheet metal
3 · tig welding sheet metal
4 · sheet metal welding process
5 · miller welding sheet metal
6 · how to weld thin sheet metal
7 · how to weld sheet metal
Dress your contemporary two-story home with house numbers that marry modern lines with surprising materials. Below, we share seven striking options including, but not limited to: a sophisticated yet friendly Arial typeface, a white acrylic design and a silver laser-cut plaque that celebrates negative space.

Each welding process requires specific precautions and equipment setup for a successful sheet metal weld. So, let’s discuss the preparation needed for each arc welding process before proceeding to the common problems with thin gauge welds. See moreNow that we’ve covered the essential considerations for different arc welding processes, let’s discuss how to prevent and fix common . See moreWelding thin metal is challenging. There is no denying that. But, if you practice and use the tips we shared in this article, you’ll get the best chance for success. After you inevitably burn through some scrap sheets of metal and warp others, you’ll gain more experience and learn . See more
Preventing burn-through and warping when welding sheet metal is all about controlling the heat. Choose the right welding process and filler metal, and follow these . In this video I demonstrate how to set up your mig welder so you can weld thin sheet metal. We also showed in this video how to make your pattern, fit and we. To weld thin metal, choose an appropriate process (TIG or MIG with low amperage), use a smaller diameter wire or filler rod, and adjust travel speed to prevent burn-through. Employ a pulsing technique, stitch welding, or .
It is recommended that a welder should use .023- or .024-inch wire for light gauge sheet metal work. However, if you are dealing with materials that are 18-gauge or thicker, one . Minimizing burn-through and distortion is essential to obtaining a good weld when gas metal arc welding thin-gauge materials. Gas metal arc welding (GMAW) is an effective method for joining light-gauge metals such as .
MIG is the ideal method for welding a 20-gauge metal sheet. The process is fast and simple to use. The only downside is you cannot use it for outside welding as the wind can easily blow out your shielding gas. Welding thin sheet metal can be challenging because you need to obtain adequate fusion while preventing distortion and burnthrough. The key skill is to control the heat across the sheet metal to prevent defects. This guide . This article provides a detailed view of the various methods used in welding sheet metal, including their advantages and applications. It also provides vital tips to note when welding thin sheets of metal to obtain the best outcomes.
welding sheet metal using mig
There are many different methods for sheet metal welding, but the three we are going to discuss are MIG (metal inert gas), TIG (tungsten inert gas), and laser welding. The method used will .Which metal transfer mode uses a high welding voltage that ultimately causes fine droplets of electrode wire to be carried axially to the molten weld puddle? Spray transfer. Short-circuiting metal transfer is the best mode to use for welding ----? light-gauge sheet metal. FCAW welds made with CO2 shielding gas produce____? Deep penetration. For thin sheet metal welding it can be 30 ampere while for thicker (e.g. 1/8” square groove weld)- it can go up to 220 ampere for example. GMAW-S gives low heat and makes it easy to use in all positions on sheet metal, low . It is ideal for hobby welders that can complete their sheet metal welding job without requiring a high duty cycle. Best Value for Money. Hobart Handler 140 MIG Welder. Can Weld Up to 1/4" Mild Steel; 20% Duty Cycle at .
When welding thin sheet metal, do not try to run one bead right across the joint. This will cause too much heat to build up. Instead, run a series of short welds at different points in the metal that eventually join together. Leave the metal to cool for a second or two between welds to help the heat dissipate. If you are welding light gauge sheet metal, a .023- or .024-inch wire is the best option. But if the gauge sheet metal is slightly thicker, you can use a .030-inch Mig wire. 2. Higher Argon Gas for Mig Welding Sheet Metal. It is a solid rule of thumb to use an increased amount of argon for the shielding gas. The argon gas should be between 75 .
It is recommended that a welder should use .023- or .024-inch wire for light gauge sheet metal work. However, if you are dealing with materials that are 18-gauge or thicker, one should be able to use .030-inch welding wire. As for mild steel, wires such as ER70S-6 are recommended for use as they have a weld buddle that wets out nicely .
Stick welding sheet metal can be done by welding DC electrode negative with 20-40A which is about the the lowest amperage settings that still allows to strike an arc. Suitable electrodes are E6011 for rusty or painted surfaces or E6013 for clean surfaces. Rod diameter shall be as thin as possible, so 1/8″ or 1/16″ diameter electrodes are .Which metal transfer mode uses a high welding voltage that ultimately causes fine droplets of electrode wire to be carried axially to the molten weld puddle. short-circuiting transfer. Short-circuiting metal transfer is the best mode to use for welding. light-gauge sheet metal. FCAW welds made with CO2 shielding gas products produce. deep .which metal transfer mode is uses a high welding voltage that ultimately cause fine droplets of electrode wire to be carried axially to the molten weld puddle? short-circuiting transfer. Short-circuiting metal transfer is the best mode to use for welding. light-gauge sheet metal. FCAW welds made with CO2 shielding gas produce. deep penetration.
I am learning TIG welding - getting better. I have a scenario where I need to weld a bolt (as a stud) to a Jeep firewall. The bolt is a flat head allen bolt, like a furniture bolt. I don't want to blow a hole in the firewall or melt the bolt trying to weld it. For practice, I welded a couple of hex bolts to some 1/4" stock and burned up the bolt head.Before CMT, welding light-gauge sheet metal was always more of an art form than an engineered production process. MIG and TIG create excessive amounts of heat, which can cause meltback and warping, often ruining the work pieces and causing a high internal reject rate. This raised not only our internal costs but also the odds of your job being late.
MIG welding sheet metal requires a combination of technical expertise, precision, and dedication to continuous improvement. By understanding the nuances of sheet metal welding, considering critical factors, and honing your welding techniques, you can achieve exceptional weld quality and elevate the overall standard of your welded assemblies.Welding sheet metal can be a nightmare with all of the warping and blow through caused by excessive heat. In this video I will be showing you 4 different te.
welding sheet metal
Welding Sheet Metal. Welding is an essential process of joining metals together. Different techniques are employed to bond sheet metal, including laser, gas, and tig welding. To ensure successful welding, clean the metal surface and select the appropriate filler metal. Keep the heat low and work in sections, making sure to remove any impurities. Imagine a welding process that minimizes distortion, enhances precision, and improves efficiency. Laser welding technology for sheet metal does exactly that, revolutionizing industries from automotive to high-tech . On this episode of Make It Kustom, I continue to repair the rust on the GMC G10 boogie van. We talk in depth about technique for repairing rust and welding o. You'll never warp another panel again after watching this video. This is a realtime, step by step demonstration that shows how to mig weld sheet metal withou.
MIG welding simplifies the feeding of filler metal, making the welder’s job easier. While the specific material may not be critical, the form of the filler metal is important when working with thin sheet metal. 3. Adjust the Torch Angle. Modifying the torch angle during MIG welding significantly helps prevent burn-throughs. Most people are not familiar with this weld method. When it comes to welding light gauge sheet metal, most would prefer TIG. TIG welding is a very slow proce.Try going for a wire of .023 inches when welding sheet metal. For sheet metal, I use INE welding wire and it is just as good as their flux-cored wire, if you want, you can grab one here: https://amzn.to/37BeVJ1; While wire feed welding sheet metal, go for short bursts of welding instead of a going on a long bead. Short bursts or tacks will help .
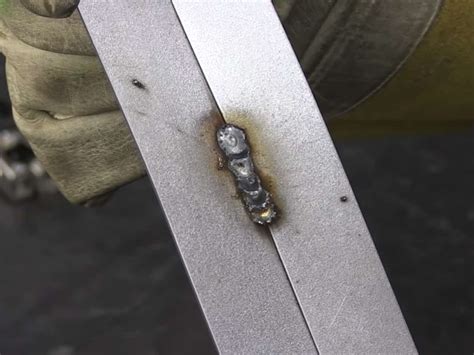
Sheet metal welding is a vital aspect of manufacturing. Read on to learn the different welding methods for the sheet metal parts. Capabilities. CNC Machining. . Generally, when working with light gauge sheet metal, 0.023 or 0.024-inch is recommended. However, a 0.030-inch wire may be ideal when welding 18 garage or thicker metals. 5.Basics in Sheet Metal Welding. Each product tells a tale of dedication, precision, and passion. To understand our story, you need to look at the sheet metal welding process, which is the basis of all our products. What is sheet metal welding? In its simplest form, welding is joining two or more metals or thermoplastics using heat, pressure, or . Welding sheet metal can be difficult. This 2 part video explains & demonstrates the basic techniques and tips for first time sheet metal welders. LINK TO BUY.There is no hard and fast rule with the thickness under which you shouldn’t use stick welding.But there is a fair idea of what constitutes a thin metal and below which using stick welding might become difficult. A lot of people consider anything less than 3/16” to be thin so below this thickness stick welding can start creating problems or can become difficult to handle.
Hi all, I'm working on an old Datsun 1200 that when soaking wet the total weight's approx. 1600 lbs. Being light is great except the floor pans easily rust through. The metal is probably 24/26 GA. (.032 if I'm remembering my measurement right). so far I've done both butt and overlap with flange welds. It's very difficult to butt weld w/o blow thru.Sheet Metal Levin | Light Fabrication Horowhenua | Welding: Winiata & Anderson Sheetmetal are specialist metal fabricators and manufacturers, helping design and produce quality custom products across all industries. . A wide range of services is offered from sheet metal cutting and folding through to welding.
Common Mistakes to Avoid in Butt Welding Sheet Metal. While butt welding sheet metal is a valuable and versatile technique, it is not without its challenges and potential pitfalls. Understanding and avoiding common mistakes in the butt welding process is essential for achieving superior weld quality, structural integrity, and overall project .
1965 nova sheet metal
1967 oldsmobile cutlass sheet metal
CNC machining is a manufacturing process that uses computerized controls to operate and manipulate machine tools, shaping a variety of materials into custom parts and designs. There are several types of CNC machines, each with specific capabilities and applications.
welding light sheet metal|miller welding sheet metal