cold welding sheet metal Learn why MIG, pulsed MIG, TIG and pulsed TIG are the ideal choices when welding sheet metal. When welding thin metal, the main objective is to avoid warping, burn . Galvanized Steel Coil & Sheet; Galvalume Steel Coil & Sheet; Corrugated Steel .
0 · welding thin to thick metal
1 · welding 14 gauge sheet metal
2 · welder settings for sheet metal
3 · welded sheet metal manufacturing
4 · sheet metal welding methods
5 · best welding for thin metal
6 · best welder for sheet metal
7 · 18 gauge weldable sheet metal
A junction box makes that easier by allowing you to connect directly to the main breaker. This negates the need to running wire through the entire house back to the breaker, providing that the power requirements of those components .
Cold welding, commonly referred to as cold pressure welding, contact welding, or cold forge welding, is the process of joining two pieces of metal together with pressure to achieve the desired bond. There are various ways to apply . Cold welding is a process that involves joining two metal surfaces together without the use of heat. This process is also known as solid-state welding and is achieved by applying pressure to the metal surfaces until they .The cold welding process is a phenomenon where two clean metal surfaces are brought into contact and joined together without the need for heat or soldering. This happens because the atoms on the surfaces of the metal pieces bond . Learn why MIG, pulsed MIG, TIG and pulsed TIG are the ideal choices when welding sheet metal. When welding thin metal, the main objective is to avoid warping, burn .

Cold welding, or contact welding, is a solid-state welding process that requires little or no heat or fusion to join two or more metals together. Instead, the energy used for creating a weld comes in the form of pressure. Cold metal transfer (CMT) is a fusion welding process that uses a welding arc to create a joint. It’s often mislabeled as “cold welding,” causing confusion. CMT is a MIG welding process that requires about 90% less heat input than a regular MIG welding process.Cold welding, commonly referred to as cold pressure welding, contact welding, or cold forge welding, is the process of joining two pieces of metal together with pressure to achieve the desired bond. There are various ways to apply pressure to achieve the desired connection. Cold welding is a process that involves joining two metal surfaces together without the use of heat. This process is also known as solid-state welding and is achieved by applying pressure to the metal surfaces until they bond together.
The cold welding process is a phenomenon where two clean metal surfaces are brought into contact and joined together without the need for heat or soldering. This happens because the atoms on the surfaces of the metal pieces bond directly to each other through metallic bonding. Learn why MIG, pulsed MIG, TIG and pulsed TIG are the ideal choices when welding sheet metal. When welding thin metal, the main objective is to avoid warping, burn-through and excessive heat-affected zones while still ensuring the weld has enough mechanical strength for the application.Cold welding, or contact welding, is a solid-state welding process that requires little or no heat or fusion to join two or more metals together. Instead, the energy used for creating a weld comes in the form of pressure.Explore the significance of the Cold Metal Transfer (CMT) process in the welding industry, particularly in welding thin sheet metal. Understand its benefits, including low thermal input, high quality, and high productivity.
welding thin to thick metal
Cold pressure welding, also known as solid-state welding, is a joining process that relies on the application of high pressure at room temperature to create a metallurgical bond between two workpieces.
Cold Metal Transfer (CMT) welding is a welding process used for joining light-gauge sheet metal. It is preferred over conventional MIG and TIG welding methods due to its lower heat output and stability. Cold welding is a solid-state welding process that requires little or no heat to join two or more metals together. Instead, the energy used to join the materials together comes in the form of pressure.
Cold metal transfer (CMT) is a fusion welding process that uses a welding arc to create a joint. It’s often mislabeled as “cold welding,” causing confusion. CMT is a MIG welding process that requires about 90% less heat input than a regular MIG welding process.Cold welding, commonly referred to as cold pressure welding, contact welding, or cold forge welding, is the process of joining two pieces of metal together with pressure to achieve the desired bond. There are various ways to apply pressure to achieve the desired connection. Cold welding is a process that involves joining two metal surfaces together without the use of heat. This process is also known as solid-state welding and is achieved by applying pressure to the metal surfaces until they bond together.The cold welding process is a phenomenon where two clean metal surfaces are brought into contact and joined together without the need for heat or soldering. This happens because the atoms on the surfaces of the metal pieces bond directly to each other through metallic bonding.
welding 14 gauge sheet metal
Learn why MIG, pulsed MIG, TIG and pulsed TIG are the ideal choices when welding sheet metal. When welding thin metal, the main objective is to avoid warping, burn-through and excessive heat-affected zones while still ensuring the weld has enough mechanical strength for the application.
Cold welding, or contact welding, is a solid-state welding process that requires little or no heat or fusion to join two or more metals together. Instead, the energy used for creating a weld comes in the form of pressure.Explore the significance of the Cold Metal Transfer (CMT) process in the welding industry, particularly in welding thin sheet metal. Understand its benefits, including low thermal input, high quality, and high productivity.
cnc machine job salary
Cold pressure welding, also known as solid-state welding, is a joining process that relies on the application of high pressure at room temperature to create a metallurgical bond between two workpieces. Cold Metal Transfer (CMT) welding is a welding process used for joining light-gauge sheet metal. It is preferred over conventional MIG and TIG welding methods due to its lower heat output and stability.
welder settings for sheet metal
welded sheet metal manufacturing
sheet metal welding methods
best welding for thin metal
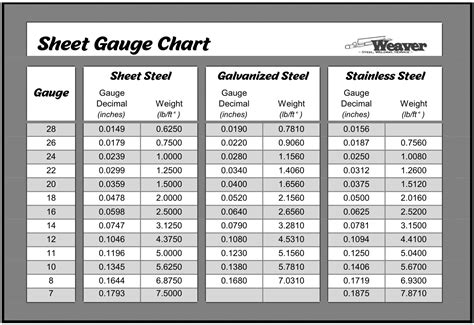
A septic tank’s distribution box (or D-box) is a container (typically concrete) that receives the septic tank effluent and re-distributes it into the network of attached drain fields and pipes. To .
cold welding sheet metal|welding thin to thick metal