how to track job expenses in metal fabrication We discuss how to accurately price steel fabrication to give your customers a competitive price that doesn’t hurt your bottom line or reputation. Shop for-and learn about-Vintage and Antique Dollhouses. Elaborate cabinet-style dollhouses (also spelled as "doll houses"), in which the rooms on one side.
0 · shop rates for metal fabrication
1 · sheet metal manufacturing costs
2 · sheet metal fabrication cost estimator
3 · sheet metal fabrication cost
4 · how to estimate metal manufacturing jobs
5 · how to calculate custom metal manufacturing
6 · custom metal fabrication labor rates
7 · custom metal fabrication jobs examples
For years, American manufacturers touted their Open-C channel frames were designed to flex, while the Japanese market reveled in their fully boxed frames, with their strength and their other advantages they had over the American market. How really true was all of this?
By tracking and comparing the actual versus estimated direct labor time for each operation, you evaluate estimating accuracy and employee efficiency. Longer-than-estimated labor time could indicate a problem, such as . All we need is a report on what the job cost. It’s the estimator’s moment of bliss: certainty of time and material expended to complete the job. .
Understanding the costs of a sheet metal part will help you evaluate the choices each supplier is making to provide their price. First, let’s take a look at some of the key components of a sheet . Via accurate job costing, many of these variables can be better handled by breaking down the entire project into smaller pieces to track . We discuss how to accurately price steel fabrication to give your customers a competitive price that doesn’t hurt your bottom line or reputation.
Here are the important steps all steel service centers & metal fabricators should take to track job costs accurately and protect their profit margins.Track job costs to assess the profitability of each project or job in your shop. Genius ERP lets you trace job costs throughout the production process, including gathering and allocating expenses related to labor, machines, materials and .
Job Costing and Tracking: Tracking costs and expenses associated with each fabrication project, including labor, materials, overhead, and other expenses, to monitor profitability and project performance.
Whether it involves welding on a jobsite or fabrication in a shop, this question can be difficult to answer. Direct costs — equipment purchases, labor hours, filler metal, and . The Fabricator is North America's leading magazine for the metal forming and fabricating industry. The magazine delivers the news, technical articles, and case histories that enable fabricators to do their jobs more . Factor in the prevailing labour rates in your geographical location or the location where the fabrication will take place. 4. Equipment and Tooling Costs: The estimation of structural steel fabrication costs should also account for equipment and tooling expenses. Fabricating structural steel components often requires the use of specialised .
Metal fabrication is integral to manufacturing, which is why so many shops and plants seek to incorporate value-adding fabrication services. Success in this manufacturing requires being able to provide a product quicker .
The Fabricator is North America's leading magazine for the metal forming and fabricating industry. The magazine delivers the news, technical articles, and case histories that enable fabricators to do their jobs more efficiently. The Fabricator has served the industry since 1970. start your free subscription The average cost of a welding fabrication job in the United States is approximately ,500, but this can vary significantly depending on the complexity and size of the project. 3. In the early 1900s, acetylene gas welding was the primary method used in welding fabrication. The Fabricator is North America's leading magazine for the metal forming and fabricating industry. The magazine delivers the news, technical articles, and case histories that enable fabricators to do their jobs more efficiently. The Fabricator has served the industry since 1970. start your free subscription If you're interested in pursuing a job in metal fabrication, it can be helpful to understand the range of opportunities open to you and the process for creating an effective resume. In this article, we define the components of a metal fabrication resume, explain how to write one, review tips for writing an effective resume and provide a .
[Total jobs won/Total jobs bid] Also called the capture rate, the win-to-bid ratio average since 2012 among survey respondents is 35 percent, though the range varies widely, depending on the fabricator’s niche. Even so, Zerio said that when a shop calculates its own win-to-bid average, it provides a good benchmark that can guide a shop’s .
37 Structural Metal Fabricators Fitters jobs available on Indeed.com. Apply to Fitter, Metal Fabricator, Fabricator/welder and more! Yes, you can use tags to track expenses. This lets you see how specific areas of your business are doing. However, I recommend using the Project feature since you're tacking multiple jobs. This makes it easy to manage your work and see their progress. Let me guide you through the steps: Step 1: Turn on projects Rob Marelli left a family-owned metal fabricating company four years ago with the intention of doing things his way. Joined by a loyal group of managers and employees, he's found success at Seconn Fabrication. In the short time the company has been open, it has earned revenues of million. And the company has done this by doing things other metal fabricating .
In this fast-paced and demanding industry, staying ahead of the curve through best practices is essential for sheet metal fabricators to thrive and succeed. Here are some ways leading fabricators are doing so today. 7 Sheet Metal Fabrication Best Practices to stay competitive and improve profitability.
Working in metal fabrications can be a satisfying career path with plenty of room for growth and advancement. If you enjoy working with your hands, paying close attention to detail and manufacturing high-quality products, you can earn a high salary for your skills.
Thank you for sharing more details, @StanleySumnerllc. I can share some clarifications, Stanley. Ensure to create a different customer project/job to track it under the customer's name (Daniel Du Brin). The new customer is different from the parent company. For example, if the project name is Plumbing, you'll have to create a new sub-customer for that job .UNDERSTANDING SHEET METAL COSTS Follow us on ... Http://www.ETMmfg.com 11 for a sheet metal fabricator are: 1. Office wages 2. Sales wages 3. Payroll taxes 4. Employee health care 5. Rent There are certainly other costs that are .For metal fabricators, this includes storage expenses, insurance, and depreciation of materials. By optimizing your inventory levels, you can reduce these costs significantly. Production Efficiency: Having the right materials readily available .

In custom metal fabrication and other job shops and custom manufacturing companies, shortening lead time is the golden road to profitable growth. . Eventually a vendor might institute a fast-track quoting process for . Benefits of Outsourcing Metal Fabrication. Outsourcing metal fabrication can significantly influence a company’s bottom line and overall efficiency. Cost-effectiveness is one of the primary reasons businesses turn to outsourcing. First and foremost, reduced labor and operational costs become evident. Especially when outsourcing to regions .Steel Projects provides a steel fabrication software including a real time production monitoring feature. . Production progress tracking at different levels. . Fabrication jobs; A color codes is applied to each desired step of production. Those colors can be seen directly in the 3D model in Steel Projects PLM to track production on the .
26 Metal Fabrication Sales jobs available on Indeed.com. Apply to Metal Fabricator, Jeweler, Heavy Equipment Sales Representative and more! . Keeps accurate and up-to-date information in the Company’s sales tracking system and controls sales expenses. . Order and track parts for corresponding jobs; Experience: Take, for example, the case of “revert”—scrap metal from the manufacturing process that can be remelted and sent back into production. Not all revert can be used immediately, particularly if the manufacturer is making many different products. The Fabricator is North America's leading magazine for the metal forming and fabricating industry. The magazine delivers the news, technical articles, and case histories that enable fabricators to do their jobs more efficiently. The Fabricator has served the industry since 1970. start your free subscription
shop rates for metal fabrication
This shop by McCorvey Sheet Metal Works will give you an idea of what a large sheet metal fabrication shop entails. Most fabrication shops will not be this large, but this will give you an idea of what is capable on a larger scale and how productivity is also related to how well a shop is organized and professionally operated.
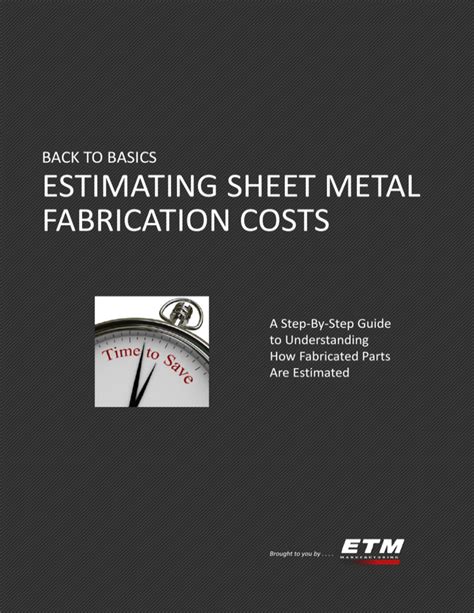
JobBOSS² is designed to help metal fabrication shops tackle the complexities of large, custom jobs, optimize production workflows, and maintain profitability. With proven job tracking, real-time scheduling, inventory management, and compliance tools, JobBOSS² offers the functionality to ensure that every aspect of your shop runs smoothly. Scheduling a custom metal fabrication operation attempts to bring order to chaos. Most fab shops don’t have the luxury of a product line, and even if they do, they likely fabricate that product on some shared resources. As in all kinds of job shops, the constraint in custom metal fabrication can move depending on the given mix of jobs on the .The cost of raw materials plays a pivotal role in sheet metal fabrication expenses. China’s dominance in manufacturing often translates to competitive material prices, thanks to extensive supply chains and economies of scale. However, fluctuations in global commodity markets and quality control issues may pose challenges for businesses .
During a late fall webcast, hosted by the Fabricators & Manufacturers Association Intl. (FMA), Steve Zerio, a partner with Novi, Mich.-based Triumph Partners, showed an eye-opening pie chart that broke down where the sales dollars go at a typical custom metal fabricator.Taking out the cost of material, direct and indirect labor, overhead, and sales .
2010 dodge caravan junction box diagram
2007 x5 electronic junction box
With the use of a junction box, it becomes easy to connect the solar panel to array. Usually cables with MC4 / MC5 connectors at the end are used. A good junction box keeps corrosion at the terminals to a minimum, as it will exclude water coming in. When purchasing solar modules, always have a look at the IP rating of the PV junction box.
how to track job expenses in metal fabrication|sheet metal manufacturing costs